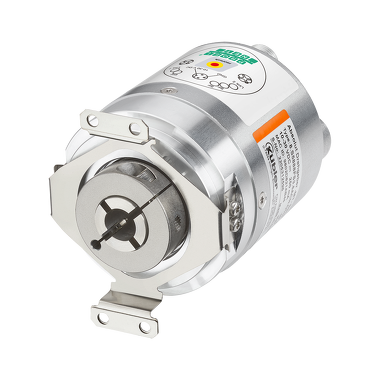
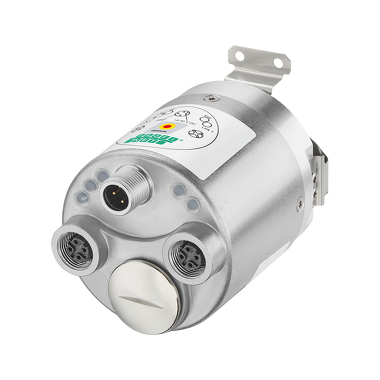
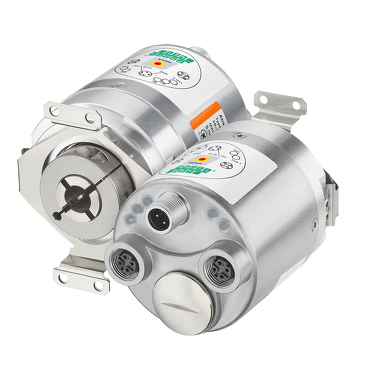
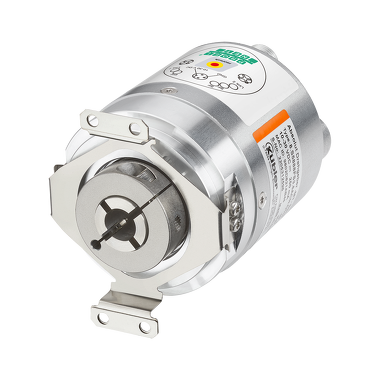
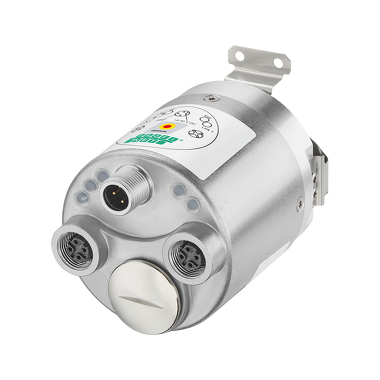
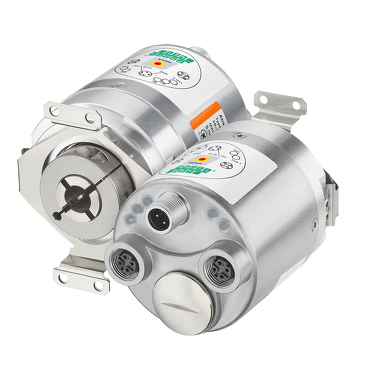
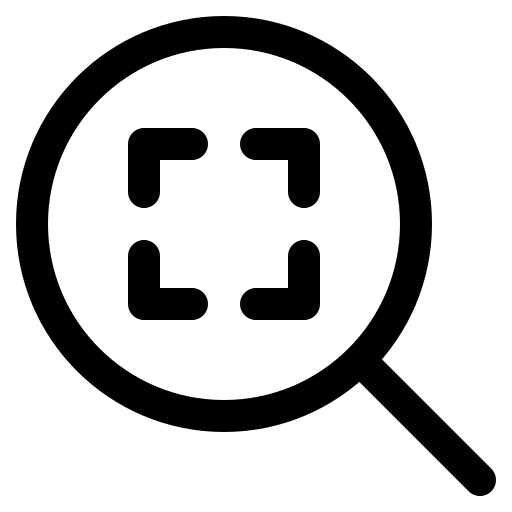
Encoders Absolute singleturn
Sendix S5878FS3
|
|





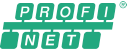
For safety applications – Sendix S58 PROFIsafe encoders
The optical absolute Sendix S58 PROFIsafe encoders are based on the new Kübler Industrial Ethernet encoder platform and are therefore already designed today for future Industry 4.0 concepts.One example of this is the integrated web server: Features or adjustments can be implemented quickly and easily at any time.
As certified SIL3 / PLe encoders with redundant design and PROFINET interface, they support the PROFIsafe profile and are predestined for safety applications.
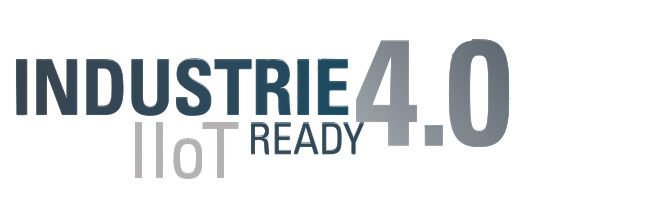
Connectivity stands for the ability to communicate additional information and / or to be integrated in a network. This can take the form of additional interfaces such as OPC-UA (e.g. for additional edge communication) or Industrial Ethernet communication as well as a digital interface such as "BISS" or "SCS open link".
Identification is the ability to transmit technical information by means of an electronic data sheet / type plate. In addition, further information about the machine can be transmitted (e.g. information about the axis where the encoder is installed). Essentially, all the information required in the application for asset management is recorded here.
Diagnostics functions provide relevant information about the condition of the product (e.g. error messages) or indirect information about the application. For example, an integrated temperature sensor can indicate that the permissible working temperature range has been exceeded. Or integrated vibration sensors provide information on the condition of the power train bearings. Highly integrated bearingless systems in particular can provide reliable information here. Log and time stamp functions in Industrial Ethernet encoders make it possible to create lifetime histograms.
Adaptability refers to adaptability, which can take place on two levels:
- At the operational level, the parameters / settings of an encoder can be changed during operation, e.g. to optimize setup processes or to eliminate measurement errors with digital signal processing.
- Software updates can be carried out at system level at any time.
The range of functions for the implementation of Industry 4.0 / IIoT concepts can be subsequently extended in order to guarantee the future viability of the system. Therefore, all Kübler fieldbus and Industrial Ethernet encoders are available with a firmware update function as standard.
Mechanical | |
---|---|
Dimension | Ø 58 mm |
Shaft type |
3/8 " hollow shaft, blind hole 10 mm hollow shaft, blind hole 12 mm hollow shaft, blind hole 14 mm hollow shaft, blind hole 15 mm hollow shaft, blind hole 1/2 " hollow shaft, blind hole |
Flange type |
Stator coupling FS Torque bracket FS, fixed Torque bracket FS, flexible Ø 58.00 mm |
Working temperature | -40 °C ... +80 °C |
Protection level |
IP65 IP67 |
Connection types |
M12 connector axial |
Max. rotational speed |
9.000 min-1 |
Weight | 450 g |
Electrical | |
---|---|
Scanning | optical |
Resolution max. |
24 bits singleturn |
Power supply |
10...30 V DC |
Interfaces |
PROFIsafe PROFINET IO |
Options | |
---|---|
on request |
|
- Robust
- Sturdy bearing construction in Safety-Lock™ Design for resistance against vibration and installation errors.
- High resolution
- Singleturn 15 bit (safe) or 24 bit (non safe).
- Safe
- SIL 3, performance level Ple, safety category Cat. 3.
- Transmission via safety telegrams 36/37, according to BP and XP.
- 100 % future-proof
- Implement features and adaptations quickly and easily.
- Cyber Security update in preparation / High system availability, protection against misuse (acc. IEC 62443).
- PROFINET IO, RT, IRT allows integration in applications with different performance requirementsorderungen.
- Supports the Isochronous Mode, can thus be implemented in networks for hard real-time requirements with clock cycles up to 500 μs.
- PROFINET v2.4.1, encoder profile V 4.2, PROFIsafe profile v2.6.1, PROFIdrive profile v4.2
- Ideal for highly synchronous applications, such as e. g. axis synchronization.
- Interoperability between many different control and drive manufacturers thanks to the PROFIdrive profile.
- Integrated web server for firmware update.
Software | ||
---|---|---|
Sendix S58x8 FS3 PROFIsafe TCI Tool ZIP ∼ 15,4 MB | 07.2025 |
|
|
PRONETA - PROFINET Network Analyzer Tool |
Website |
Product Certificates | ||
---|---|---|
UL CoC USA/ Canada - Encoders PDF ∼ 503,1 KB | 07.2025 |
EN |
|
Sendix F58xx PROFINET IO PDF ∼ 121,8 KB | 07.2025 |
EN |
|
Sendix S58xx_FS3 PROFIdrive PDF ∼ 75,3 KB | 07.2025 |
EN |
|
Sendix S58x8FS3 - EC type-examination certificate PDF ∼ 664,6 KB | 07.2025 |
EN |
|
Salt spray test ManufacturersDeclaration PDF ∼ 39,6 KB | 07.2025 |
DE EN |
|
S58x8 FS3 PROFIsafe PNO PDF ∼ 73,8 KB | 07.2025 |
EN |
YouTube Video | ||
---|---|---|
Integration of an S58x8FS3 PROFIsafe Encoder in TIA Portal |
Website |
Accessories
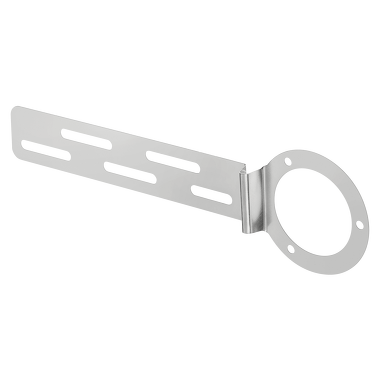
Torque stop, flexible
For hollow shaft encoders
with flange ø 58 mm
Mounting radius 39.5 ... 142.75 mm
Designed for functional safety technology.
For applications with axial and radial play at low dynamics.
Scope of delivery
- Torque support (stainless steel)
- 3 M3x6 screws for mounting on the encoder
Connection to the application (not included in delivery)
- 1 screw
8.0010.4047.00FS |
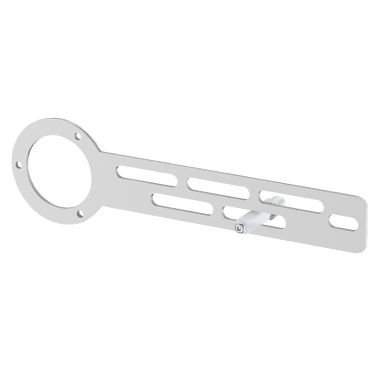
Fastening arm set, rigid
For hollow shaft encoderswith flange ø 58 mm
Mounting radius 32.5 ... 143.5 mm
Designed for functional safety technology.
For applications with very low axial and radial play at low dynamics.
Scope of delivery
- Torque support (stainless steel)
- 3 screws M3x6 for mounting to the encoder
Connection to the application (not included in delivery)
- 1 torque pin 8.0010.4049.0075
8.0010.4051.00FS |
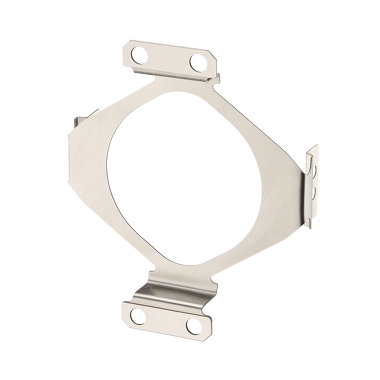
Stator coupling (FS)
For hollow shaft encoders
with flange ø 58 mm
Mounting radius 31.5 mm
Designed for functional safety technology by 4-screw principle.
Scope of delivery
- Stator coupling (stainless steel)
- 4 screws M3x6 for mounting to the encoder
Connection to application (not included in delivery)
- 4 screws
8.0010.40B2.00FS |
Cables and connectors

M12 Connector with cable , mit Edelstahl Überwurf
Preassembled cable set
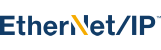
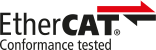
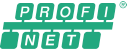
1 x 4 x AWG22 mm2