Industry 4.0 / IIoT
Encoders and Slip Rings for Industrial Internet of Things (IIoT)
The implementation of IIoT concepts in practice is one of the central challenges for every development engineer. The definition of individual concepts is the first step. In concrete terms, this means: which of the possibilities offered by IIoT should be used?In addition to a wide range of "Industry 4.0 / IIoT ready" encoders and slip rings, Kübler also offers support during implementation.
Industry 4.0 / IIoT ready
Networked and intelligent products are a prerequisite for IIoT. They are able to say:"Who am I? Where am I? How do I feel?"
"Industry 4.0 / IIoT ready" means: In addition to the classical measuring task and transmission of measured values of an encoder, in addition to the transmission of power, signals and data of a slip ring, the Industry 4.0 / IIoT ready products must also provide further functionalities for networking the products and for collecting or transmitting additional information.
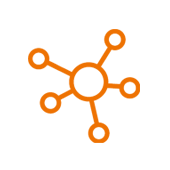
Connectivity
Connectivity stands for the ability to communicate additional
information and / or to be integrated in a network. This can take the
form of additional interfaces such as OPC-UA (e.g. for additional
edge communication) or Industrial Ethernet communication as well
as a digital interface such as "BISS" or "SCS open link".
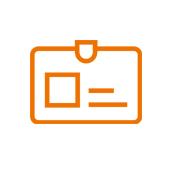
Identification
Identification is the ability to transmit technical information by
means of an electronic data sheet / type plate. In addition, further
information about the machine can be transmitted (e.g. information
about the axis where the encoder is installed). Essentially, all the
information required in the application for asset management is recorded here.
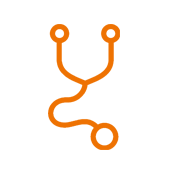
Diagnostics
Diagnostics functions provide relevant information about the condition of the product (e.g. error messages) or indirect information about the application.
For example, an integrated temperature sensor can indicate that the permissible working temperature range has been exceeded. Or integrated vibration sensors provide information on the condition of the power train bearings.
Highly integrated bearingless systems in particular can provide reliable information here. Log and time stamp functions in Industrial Ethernet encoders make it possible to create lifetime histograms.
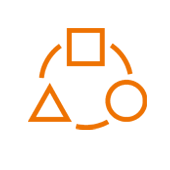
Adaptability
Adaptability refers to adaptability, which can take place on two
levels:
- At the operational level, the parameters / settings of an encoder can be changed during operation, e.g. to optimize setup processes or to eliminate measurement errors with digital signal processing.
- Software updates can be carried out at system level at any time.
concepts can be subsequently extended in order to guarantee the
future viability of the system. Therefore, all Kübler fieldbus and
Industrial Ethernet encoders are available with a firmware update
function as standard.
Asset-Management
Which Industrie 4.0 functionalities an asset needs to be "Industrie 4.0 ready" depends on the overall concept. The decisive factor is the role assigned to the asset. Either as an independent Industrie 4.0 object or as part of it. This determines whether the asset must have its own management shell or is integrated into an existing management shell. 4 kuebler.com/industry-4-0 An asset with its own management shell not only has functions at the "field level" but also at the "control level" and even up to direct edge communication. Most often, however, an asset is integrated within an object, such as in a powertrain. In this case, the question is which of the elements in the object gets the management shell and also takes over the management functions. An asset can fulfill this role (completely or partially) by having the electronic data sheet contain information not only about the asset itself, but about the entire powertrain. Basically, the management shell maps the virtual representation of the product (digital twin) and the technical functions. This enables a wide range of use cases, from simulation to asset management.
Use-Cases
Industry 4.0 opens up new perspectives and new business ideas. Compared to the current automation world, which is mainly device-oriented, Industrie 4.0 offers a holistic system view. Furthermore, the technology enables manufacturer-independent access to device data, additional standardized services, and simplified device administration. Implementation should take place step by step and be based on practical applications or implementations (use cases). We therefore recommend defining the individual use cases first and planning the technical implementation based on this.
Digital nameplate
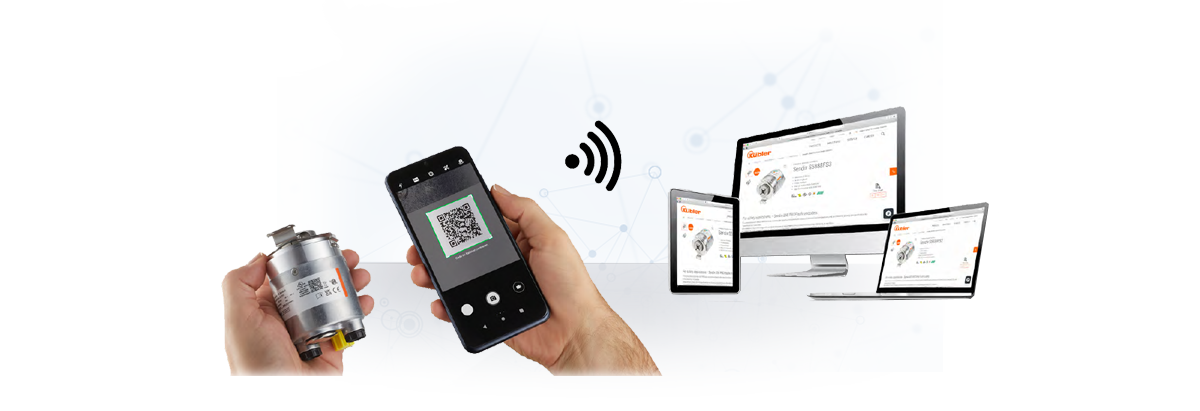
Today's physical nameplate, which forms a legal binding for the identification of a device without further aid, is included on almost every product with all relevant information. With digitization, the pure analog nameplate is a thing of the past. Complexity and diversity of variants can be eliminated by outsourcing a lot of information.
The digital nameplate is the basis for many other use cases of the digital twin.
- Sustainability (forms the path to "paperless documentation").
- Key for further product services such as "Predictive Maintenance
- Mapping of characteristic values such as "CO2 footprint" or "MTTF failure probabilities
Benefits at a glance
- Unlimited amount of information
- Fast access to information
- Reduces time and costs
- Sustainability
- Clear and dynamic information
- Global transparency
Digital twin
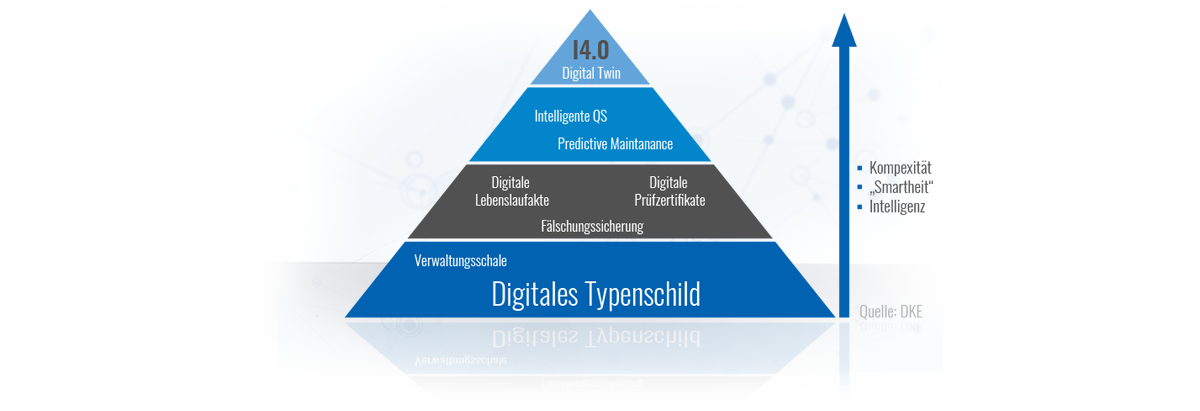
The digital twin digitally mirrors a physical product, making it easier to realize various new possibilities. The digital twin forms the top level in complexity, smartness and intelligence with regard to Industrie 4.0.
The basis is the management shell of an asset, which reflects the corresponding product. The management shell contains various submodels such as asset identification, documentation, information on certification and quality, and much more. Depending on the complexity of the asset, simple use cases can also be realized with just a few submodels.
- Asset Onboarding
- Interoperability of components, cross-manufacturer
- Digital nameplate
- Concept and design of new machines / products
- Virtual commissioning / remote commissioning support
- Process simulation
- Asset Management / Machine Book
- Update/Upgrade in the field
- (Big) Process Data Management
- Live Monitoring
- Predictive Maintenance
- Product Carbon Footprint (PCF)
- Energy Monitoring / Energy Saving Mode
- Material comliance
- Material declaration
- Waste prevention