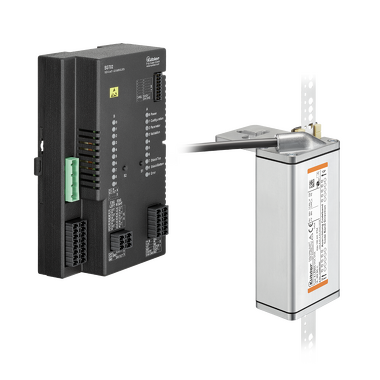
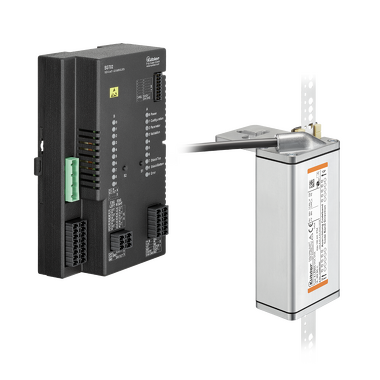
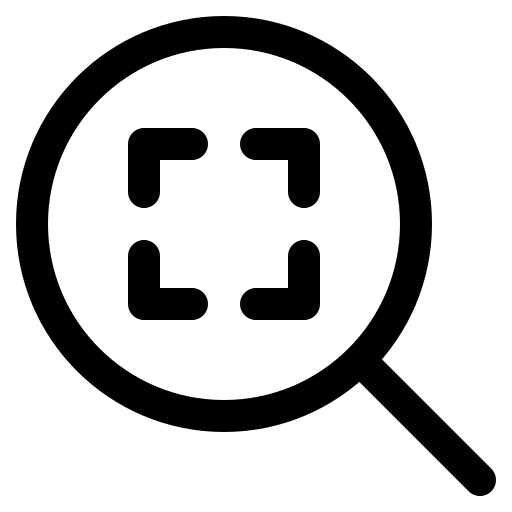
Shaft copying systems
Safe System LES03 / SGT02
|
|

To trigger electromechanical safety gears, the SIL3-certified sensor Ants LES03 can be combined with the SIL3-certified Safety Gear Trigger SGT02. This means that classic mechanical solutions with all the relevant components can be replaced. This reduces both the complexity in the installation process and the number of components in the safety circuit of the elevator system.
The state of the safety gear is constantly monitored by the SGT02 and can also be safely and easily reset after safe tripping. The safe system not only provides a high level of safety for passengers, but also realizes refuge spaces during the installation and maintenance of the elevator systems (shield mode).
Perfectly suited for the modernization of elevator systems!
Mechanical | |
---|---|
Measuring system | Shaft copying systems |
Electrical | |
---|---|
Interfaces |
CANopen-Lift |
Electronic overspeed governor
In combination with the sensor Ants LES03, the SGT02 can replace traditional mechanical overspeed governors.
Control-independent
The electromechanical safety gear is triggered independently of the control system, making the system ideal for modernization projects.
Absolute position detection
In addition to the function as electronic speed limiter, the 100% slip-free recorded position data can optionally be transmitted to the control via CANopen Lift. CAN/SSI/RS485 are also possible on request.
Overspeed
When the Ants LES03 sensor detects an overspeed, the SGT02 triggers the electromechanical safety gear. The system can be combined with different safety gears available on the market.
Condition monitoring and reset
The SGT02 also takes over the monitoring and resetting of the respective safety gear. In addition to direct evaluation, the status information can also be processed by a control system if required.
Establishment of refuge spaces (Shield-Mode)
In addition to safety for assembly personnel in accordance with the requirements of EN 81-21, the Shield mode of the SGT02 sets new standards for the safety of installation, service and maintenance personnel. Even during scaffold-free assembly, the system independently forms position- and speed-dependent refuge spaces.
Self learning system
Due to the respective highest and lowest approached position in the elevator shaft, refuge spaces are automatically produced.
Easiest validation
From plant approval to annual inspection - the reduced complexity simplifies validation processes and guarantees the highest safety standards.
Visual and audible status indication
All safety-relevant parameters can be checked quickly. The simple menu navigation as well as visual and acoustic assistance will inspire not only installers but also approved inspection agencies (ZÜS).
Accessories
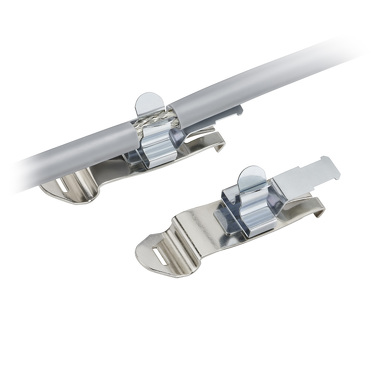
EMC shield terminal
For EMC-compliant installation of the encoder cable.- Mounting on top hat rail
- Shield diameter
- Weight approx. 7.4 g
- Clamp (spring steel, galvanized)
- Foot (spring steel)
8.0000.4G06.0312 |
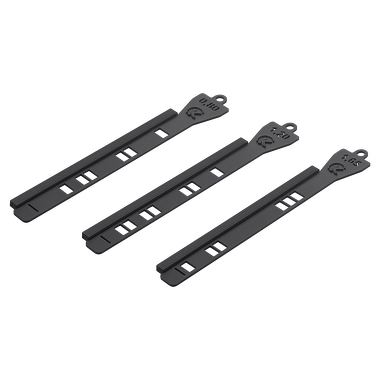
Configuration strips
The configuration strip for the respective rated speed is inserted into the LES03 sensor during commissioning. An LED visualizes the respective taught-in rated speed with a flashing pattern. In this way, the certifying agency can also validate the configuration at any time.
Corresponding configuration strips are available for different rated speeds.
8.CS.1111.XXX |
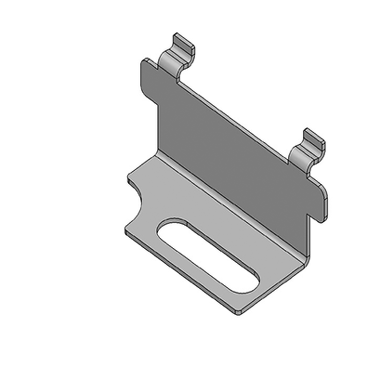
Locking element
The locking element is used for fastening the slides in the Ants LEB02 and Ants LES02 sensors.The locking element is to be replaced in case of deformations or damages.
Scope of delivery:
1 x locking element
1 x oval head screw M3.5 x 12
8.LEX.ZB.0013 |