Industrie 4.0 / IIoT
Codeurs et collecteurs tournants pour l'industrie 4.0 / IIoT.
La mise en œuvre des concepts de l'industrie 4.0 / IIoT dans la pratique constitue un défi majeur pour chaque ingénieur de développement. Dans ce cadre, la première étape est la définition des différents concepts de l'industrie 4.0 / IIoT. Ceci signifie concrètement : auxquelles des possibilités offertes par l'industrie 4.0 / IIoT faut-il faire appel?
Kübler offre, en plus d'une vaste gamme de codeurs et de collecteurs tournants prêts pour l'industrie 4.0 / IIoT, son assistance pour leur mise en œuvre.
Prêts pour l'industrie 4.0 / IIoT
Des produits intelligents en réseau sont un préalable indispensable pour l'industrie 4.0 / IIoT. Ils sont en mesure de dire : « Qui suis-je ? Où suis-je ? Quel est mon état ? ».
« Prêts pour l'industrie 4.0 / IIoT » signifie : les codeurs, en plus de leur tâche classique de mesure et de transmission des valeurs mesurées, les collecteurs tournants, en plus de la simple transmission de courant, de données et de signaux, doivent apporter d'autres fonctionnalités pour la mise en réseau des produits et pour la collecte et la transmission d'informations supplémentaires.
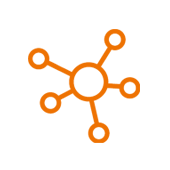
La Connectivité
La Connectivité est la capacité à communiquer des informations supplémentaires et / ou à se mettre en réseau. Ceci peut se réaliser sous la forme d'interfaces complémentaires comme OPC-UA (p. ex. pour une communication EDGE additionnelle), d'une communication par Ethernet industriel, ou d'une interface numérique comme BiSS ou SCS open link.
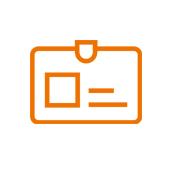
L'identification
L'identification est la capacité de transmettre des informations au moyen d'une fiche technique / d'une plaque signalétique électronique. D'autres informations concernant la machine peuvent aussi être transmises (p. ex. des informations sur l'axe d'entraînement sur lequel le codeur est monté). Pour l'essentiel, toutes les informations nécessaires dans l'application pour la gestion des équipements sont collectés ici.
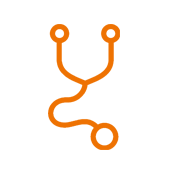
Diagnostic
Les fonctions de diagnostic fournissent des informations importantes sur l'état du produit (p. ex. messages d'erreur) ou des informations indirectes sur l'application. Par exemple, une sonde de température intégrée peut indiquer que la plage de température de fonctionnement admissible a été dépassée. Ou des capteurs de vibrations intégrés informent sur l'état des roulements de la chaine cinématique.
Ce sont justement les systèmes sans roulements hautement intégrés qui peuvent fournir des informations fiables. Des fonctions de journal et d'horodatage incorporées dans des codeurs Ethernet industriel permettent la réalisation d'histogrammes de durée de vie.
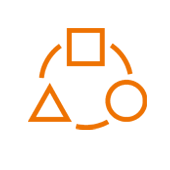
L'adaptabilité
L'adaptabilité désigne la capacité d'adaptation, qui peut agir à deux niveaux :
- Au niveau opérationnel, il est possible de modifier les paramètres / les réglages d'un codeur pendant son fonctionnement, p. ex. pour optimiser les opérations de réglage ou pour éliminer des erreurs dans les mesures avec retraitement numérique du signal.
- Au niveau système, les mises à jour du logiciel sont possibles à tout moment.
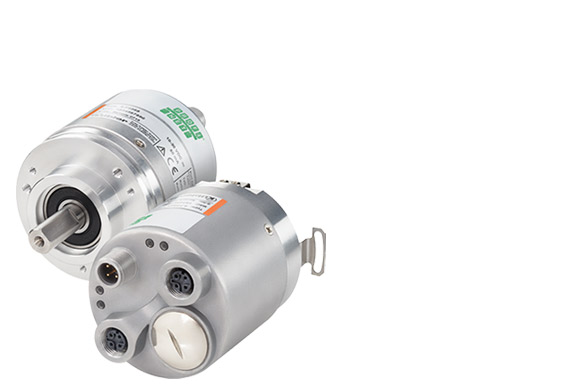
Codeurs - prêts pour l'industrie 4.0 / IIoT
Les fonctionnalités de l'industrie 4.0 / IIoT qui permettront à un codeur d'être prêt pour l'industrie 4.0 / IIoT dépendent du concept général dans lequel il sera intégré. Le rôle affecté au codeur est ici déterminant. Soit comme un objet connecté indépendant ou comme une partie d'un objet. Ce point déterminera si le codeur doit disposer de son propre système d’administration ou s'il sera intégré dans un système d’administration existant.
Un codeur disposant de de son propre système d’administration a des fonctions « Field level » (niveau terrain), mais aussi « Control level » (niveau contrôle), ou jusqu’à la communication directe Edge. Au niveau de configuration maximal, ce codeur peut par exemple être un codeur Ethernet industriel avec serveur web intégré et protocole OPC-UA supplémentaire. Cependant, le codeur est le plus souvent intégré dans un objet, par exemple un entraînement. L'objet industrie 4.0 / IIoT est alors un axe d'entraînement composé d'un moteur, d'un réducteur, d'un codeur, d'un frein, d'un variateur, etc. Dans ce cas se pose la question de l'élément de l'objet qui se verra affecter le système d’administration et qui prendra en charge les fonctions de gestion. Le codeur peut remplir cette fonction (entièrement ou en partie) en mémorisant dans la fiche technique électronique, en plus des informations sur le codeur lui-même, des informations sur l'ensemble de l'entraînement. Il peut s'agir par exemple de données du moteur, d'informations sur la localisation, etc. En principe, le système d’administration est la représentation virtuelle du produit (son jumeau numérique) et des fonctions techniques. Une large palette de cas d'utilisation, allant de la simulation jusqu'à la gestion des équipements, est ainsi possible.
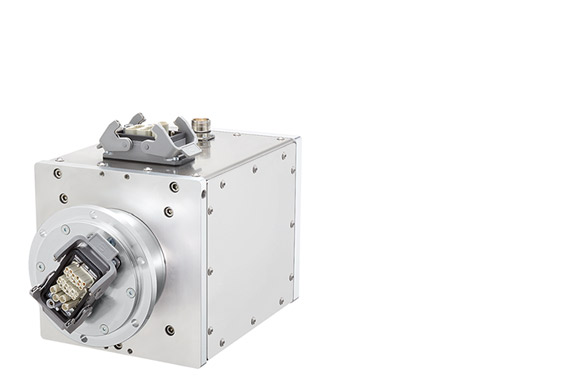
Les collecteurs tournants comme facilitateurs de l'industrie 4.0 / IIoT
Les collecteurs tournants sont la solution optimale pour la transmission de courant, de signaux, de données et de fluides comme l'air comprimé ou l'huile hydraulique d'un élément fixe vers un élément tournant d'une installation / d'une machine.
Les collecteurs tournants pour la transmission de l'Etherhet industriel permettent la mise en œuvre des concepts de l'industrie 4.0 / IIoT dans les moindres recoins d'une machine. Kübler offre également des solutions sans contact pour les applications exigeant une disponibilité maximale. Les collecteurs tournants sont des composants hautement intégrés de machines complexes. Ils permettent ainsi de fournir des informations particulièrement nombreuses et fiables sur l'état de la machine et ses besoins en termes de maintenance. C'est pourquoi Kübler les transforme en « facilitateurs pour l'industrie 4.0 / IIoT » en intégrant des systèmes de capteurs dans ses collecteurs tournants intelligents, sans que ceux-ci nécessitent pour autant davantage d'espace pour le montage. La mesure exacte et la surveillance de mouvements d'axes, de vibrations et de la température, combinées à l'enregistrement d'histogrammes tout au long de la durée de vie, fournit toutes les informations nécessaires à la surveillance d'état. Des fonctions de gestion des équipements sont supportés au moyen de fiches techniques électroniques spécifiques aux machines. Ces deux caractéristiques sont essentielles à la mise en œuvre d'une maintenance prédictive efficace ; elles permettent également l'offre de nouveaux services tels que p. ex. le « Plateforme en tant que Service (PaaS) ». Ainsi, d'un élément de transmission passif, le collecteur tournant devient un composant actif de l'industrie 4.0 / IIoT.
Cas d'utilisation
L'industrie 4.0 / IIoT ouvre de nouvelles perspectives et de nouvelles idées commerciales. Comparée au monde de l'automatisation actuel principalement orienté sur les composants, l'industrie 4.0 / IIoT offre une vision globale du système. De plus, la technologie permet un accès indépendant des fabricants aux données des appareils, des services standardisés supplémentaires et une gestion simplifiée des appareils. La réalisation doit se faire pas à pas et se baser sur des applications ou des mises en œuvre concrètes (cas d'utilisation). C'est pourquoi nous recommandons de définir dans un premier temps les différents cas d'utilisation et d'en dériver ensuite la mise en œuvre technique.
du point de vue du fabricant de l'appareil, de celui du partenaire de service (installation, mise en service et maintenance), et de celui de l'exploitant (propriétaire de l'usine).
Bien que la maintenance prédictive soit très souvent citée en relation avec la mise en œuvre pratique de l'industrie 4.0 / IIoT, elle n'est qu'un parmi de nombreux cas d'utilisation. C'est lors de la définition des cas d'utilisation que les nombreux avantages de l'industrie 4.0 / IIoT deviennent visibles.
Gestion des équipements
Il s'agit ici de la description du système avec la fiche technique, la description fonctionnelle et les informations sur la localisation, mais aussi de la référence directe à des informations disponibles dans le cloud comme des données CAO et des informations sur le cycle de vie. En bref, de tout ce qui est nécessaire pour la création d'un jumeau numérique.
Interopérabilité
Comprend tous les opérations types de communication indépendantes du système et entre systèmes, jusqu'à la communication avec le cloud. Ainsi, aussi bien des appareils individuels que le cloud (cloud appareils et cloud système) deviennent des parties intégrantes de la communication entre l’OT (technologie d’exploitation) et l’IT (technologie de l’information).
Diagnostics / Traçabilité des données
La mesure, la surveillance et la visualisation de process critiques permettent la collecte des données, leur exploitation et leur préparation pour les Big Data. Ces données constituent la base de la maintenance prédictive ou de la gestion de l'énergie, mais aussi de simulations ou d'une mise en service plus efficace d'appareils, de machines et d'installations.
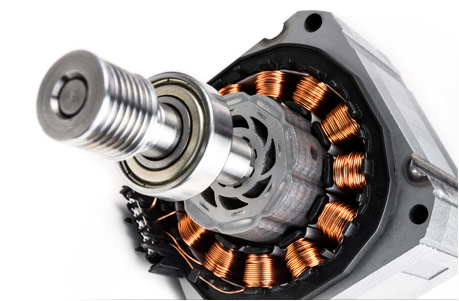
Mise en service d'une chaine cinématique avec des codeurs Ethernet industriel
L'industrie 4.0 / IIoT permet une mise en service efficace, rapide et sans erreurs. La plaque signalétique électronique du moteur et du codeur enregistrée dans le système d’administration du codeur, ainsi que les informations sur la zone de travail, la vitesse de rotation maximale, la température maximale et l'indication de la localisation, donnent à l'utilisateur toutes les informations importantes pour l'installation. Les liens vers les instructions d'utilisation, les manuels et les données CAO sont également mémorisés directement dans le codeur, permettant un téléchargement facile depuis le serveur de Kübler. Les versions de logiciel les plus récentes ou des paramétrages personnalisés peuvent être téléchargés directement par l'interface OPC-UA supplémentaire depuis le cloud appareil, sans devoir passer par la commande. Ces données peuvent être transmises à un système de gestion des équipements intégrés dans la planification de la production.
Des simulations peuvent être réalisées au préalable afin de détecter et d'éliminer toute erreur de planification. A la mise en service, le codeur supporte entre autres la fonction oscilloscope décrite dans le concept Entrainements 4.0 de ZVEI, par exemple pour une définition rapide et aisée de conditions de déclenchement spécifiques. Une mémoire des erreurs et des messages d'avertissement et d’états complets aident au diagnostic.
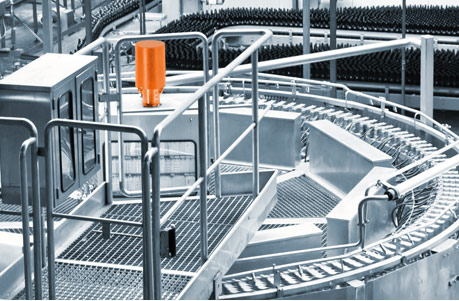
Collecteurs tournants fournissant le service Plateforme en tant que Service (PaaS)
Il est impératif pour presque toutes les machines de réduire les temps d'arrêt au minimum. Ces temps d'arrêt sont souvent influencés par les cycles de maintenance des collecteurs tournants utilisés. Comme les collecteurs tournants font partie des éléments hautement intégrés de la machine, leur entretien ou leur réparation est souvent critique.
Kübler a la solution : un système de capteurs intégré dans le collecteur tournant permet la réalisation de fonctions de surveillance d'état. Des états de fonctionnement comme p. ex. le nombre de tours, les vitesses maximale et moyenne, les températures, la durée d'utilisation, les chocs et les vibrations sont collectés et enregistrés, ce qui permet une surveillance complète de l'axe.
Les données collectées sont alors directement envoyées dans le cloud et utilisées comme base pour la maintenance prédictive. Les données exploitées permettront par exemple au service après-vente de Kübler de prévoir et de réaliser un entretien planifié du collecteur tournant. La disponibilité maximale de toute l'installation sera ainsi garantie. Ainsi, le client n'achète pas simplement le produit, mais il s'assure, grâce aux services offerts par Kübler (depuis l'installation, en passant par la mise en service, jusqu'à l'entretien ou la réparation), une transmission durable et fiable, entièrement dans l'esprit de la Plateforme en tant que Service « PaaS ».