Wystąpił błąd podczas wykonywania powierzonego zadania.
Możliwe, że nie możesz zobaczyć tej strony, ponieważ- Użyta zakładka jest nieaktualna
- Adres został wpisany z błędem
- Twoja wyszukiwarka nie odświeżyła jeszcze mapy naszej witryny
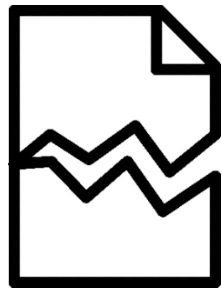
404
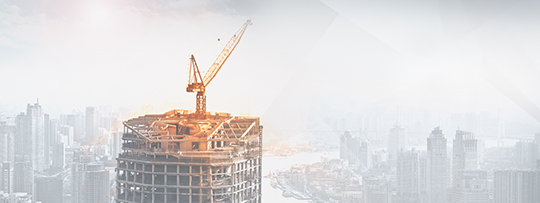
Rozwiązania dla branż
Oferujemy produkty najwyższej jakości, a także chętnie wprowadzamy modyfikacje i wykonujemy rozwiązania specjalne dla automatyki fabrycznej, branży napędów i dźwigów, automatyki maszyn mobilnych, przemysłu ciężkiego, przemysłu maszyn pakujących, jak również dla branży energii słonecznej i turbin wiatrowych.
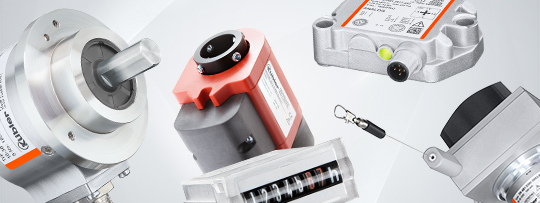
Produkty do Twojego zastosowania
Enkodery, enkodery bezłożyskowe, systemy sprzężenia zwrotnego do silników, enkodery linkowe, systemy pomiaru pozycji windy, liniowe układy pomiarowe, inklinometry, pierścienie ślizgowe, przetworniki sygnału, wskaźniki i liczniki, a także urządzenia procesowe i bezpieczne monitorowanie prędkości są do Twojej dyspozycji.